History of Composites
The concept of combining different materials in building and construction has been around since ancient history. One of the earliest examples of composite construction is around 3400 B.C., when Mesopotamians glued wood strips at different angles to create plywood. One of the many ways material technology has changed is a transition from these natural composites to man-made, synthetic composites. Advances in polymer resins and glass fibers in the 1930s, along with the development of carbon fiber in the 1960s, laid the groundwork for today’s materials used in fiber-reinforced polymer (FRP) composites. Since then, the industry has also developed expertise in specialized molding processes that allow manufacturers to tailor the unique properties of composites.
1100s
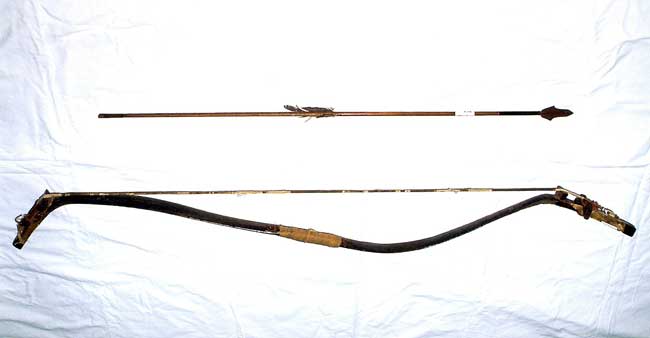
Mongols used basic composites of cattle tendons, horns, bamboo, silk and pine to build their archery bows.
1870-1890
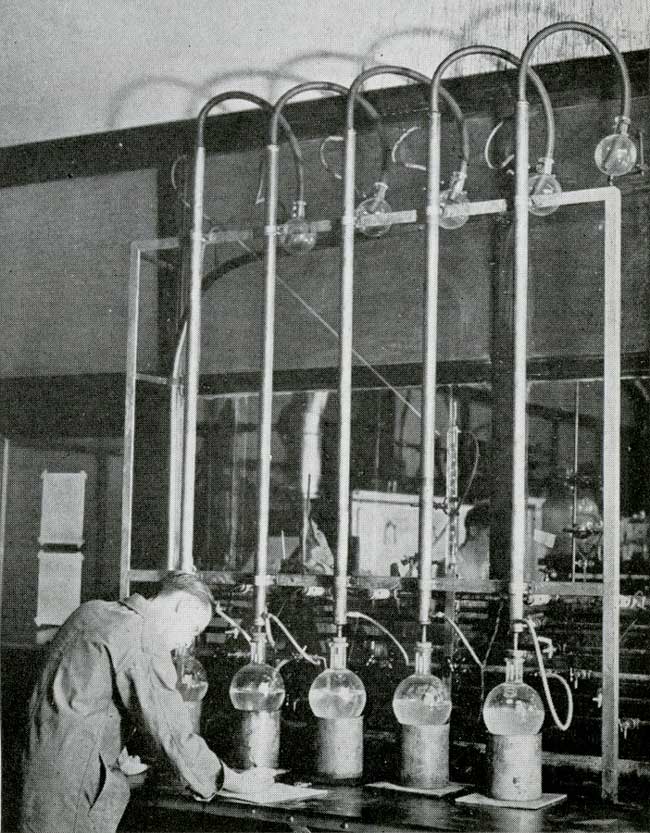
The first synthetic (man-made) resins were developed which could be converted from a liquid to a solid by polymerization. These polymer resins are transformed from the liquid state to the solid state by crosslinking the molecules.
1907
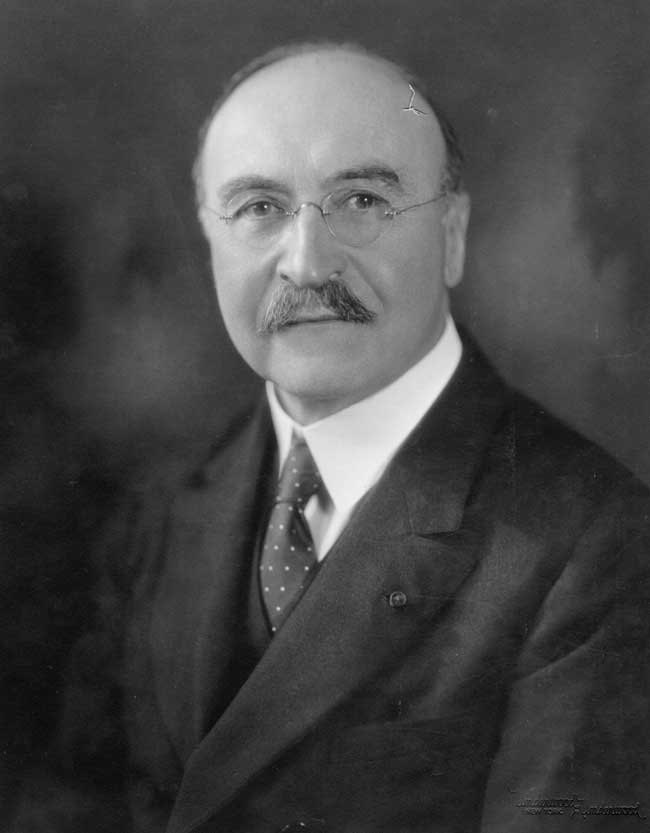
Belgian-born U.S. chemist Leo Hendrik Baekeland invents Bakelite, one of the first synthetic resins. The first commercial use of Bakelite was to make gearshift knobs in 1917 for Rolls Royce automobiles.
Early 1930s
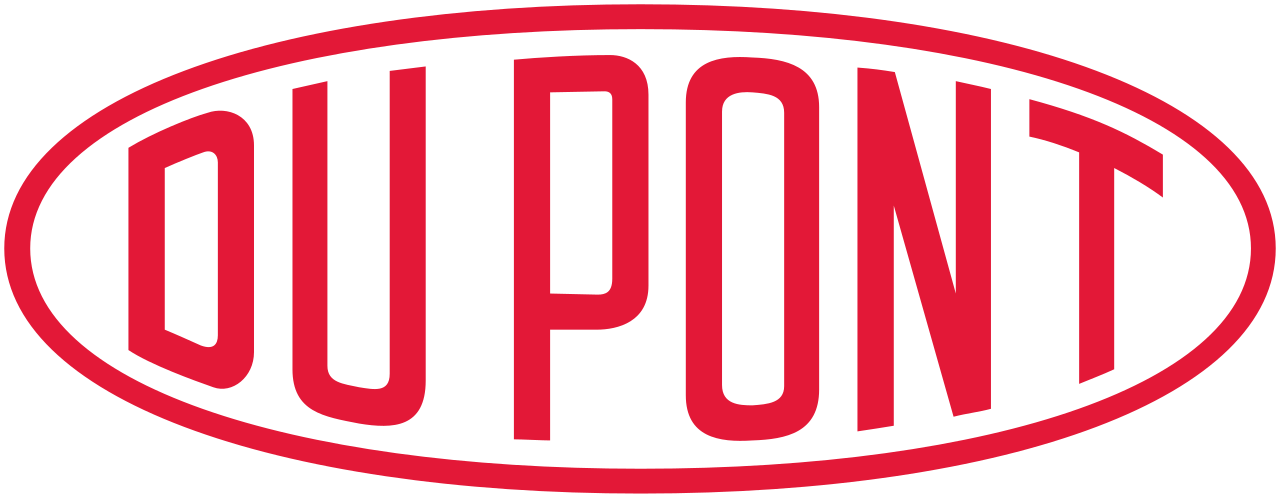
American Cyanamid and DuPont worked on polymer resins and independently formulated polyester resin for the first time.
1936
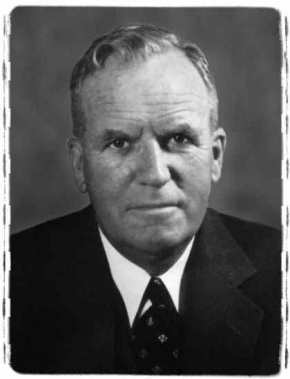
Unsaturated polyester resins were patented by Carleton Ellis. Because of their curing (or hardening) properties, they became the primary choice for resins in composites manufacturing.
Late 1930’s
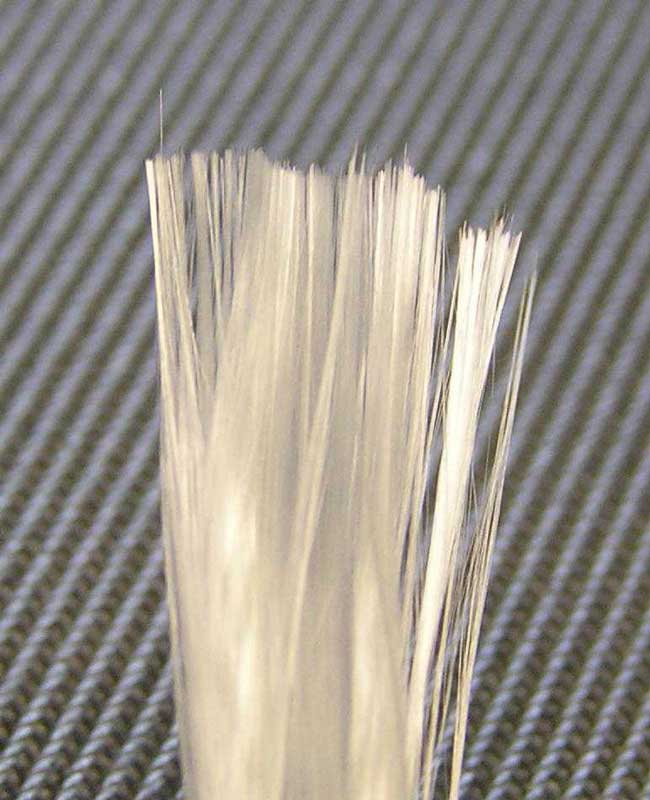
The Owens-Illinois Glass Company developed a process for drawing glass into thin strands, or fibers, and began weaving them into a textile fabric.
1942
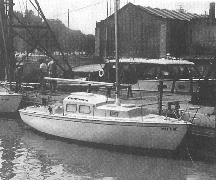
Engineer Ray Greene, who had worked for Owens-Illinois Glass, made a dinghy from fiberglass and polyester resin. The boating world would never be the same.
Mid 1940s
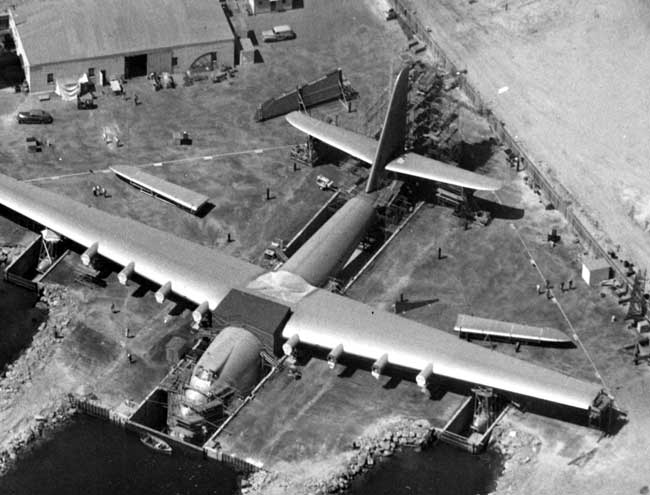
Howard Hughes used composite wing spars (thin wood layers and plastic resin) on the Spruce Goose.
1945
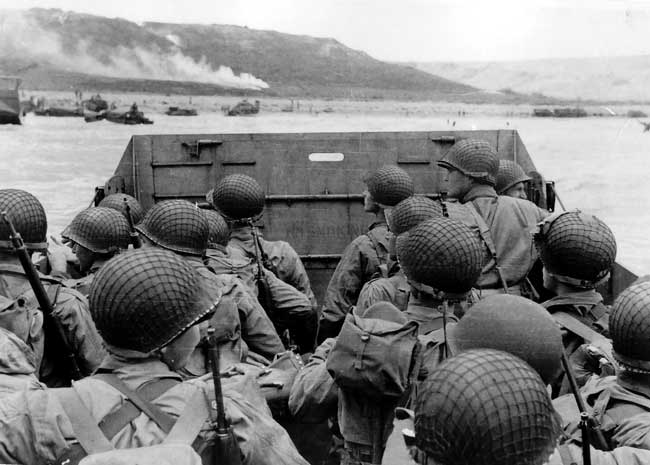
Over seven million pounds of fiberglass were used, primarily for military applications during WWII.
1948
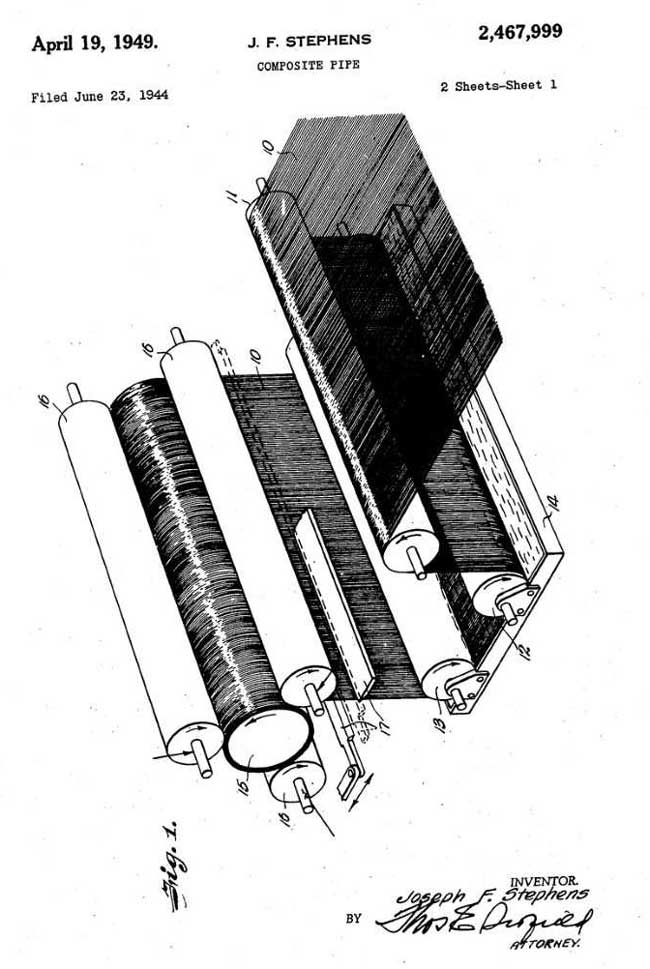
Fiberglass pipe was introduced to the oil industry, its widest area of use within the corrosion market.
1950s
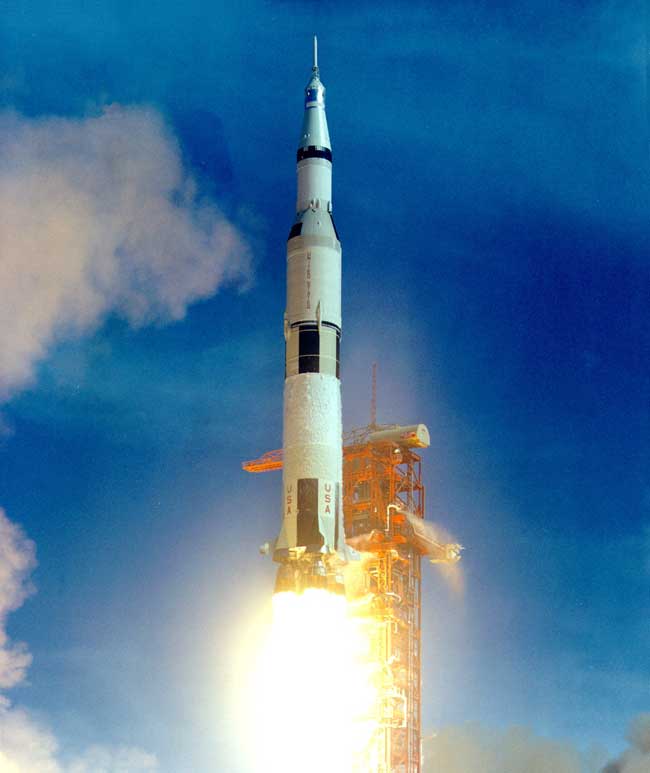
Composite use grew rapidly as boats, trucks, sports cars, storage tanks, pipes, ducts and many other products were built using composites. Manufacturing methods such as pultrusion, vacuum bag molding, and large-scale filament winding were developed. Filament winding became the basis for the large-scale rocket motors that propelled exploration of space in the 1960’s and beyond.
1966

DuPont chemist Stephanie Kwolek invented Kevlar, known best for its use in ballistic and stab-resistant body armor.
1970s
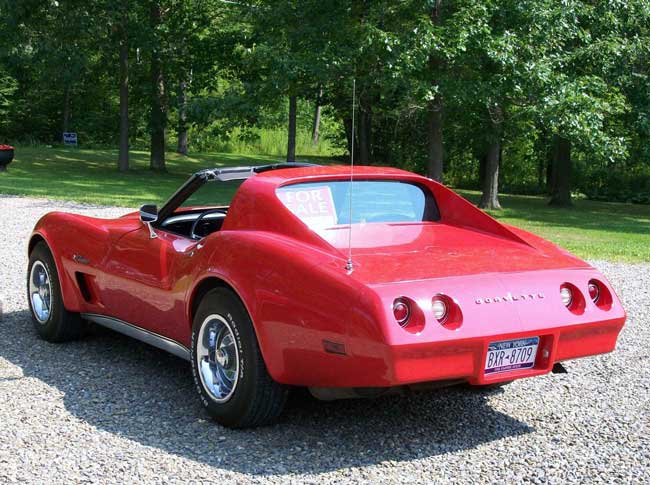
The automotive market surpassed the marine industry in composite usage as consumers became increasingly aware of composite materials, thanks in-part to the Corvette.
1970-1980s
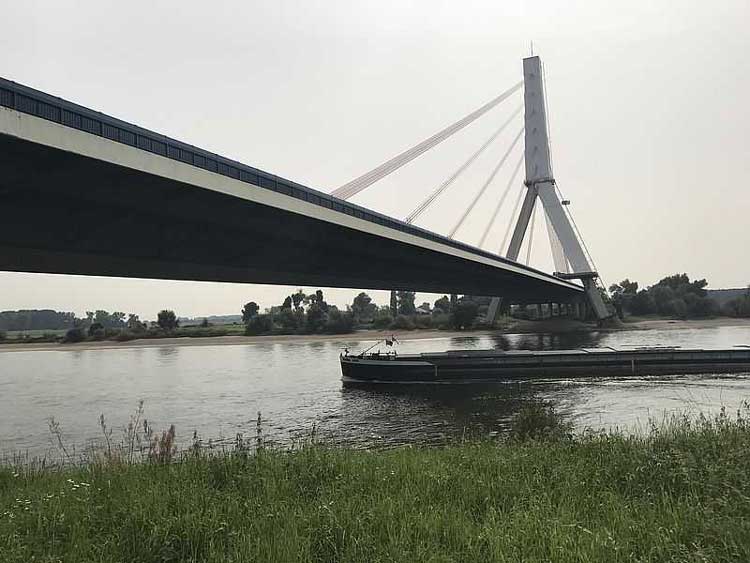
Infrastructure applications began in Europe and Asia, including the world’s first highway bridge using composites reinforcing tendons and the first all-composites bridge deck.
1990s
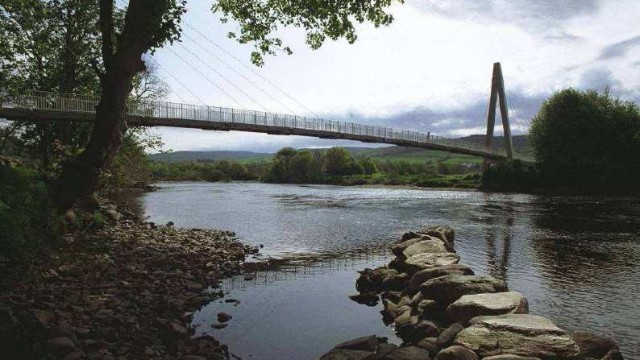
The world’s first all-composites pedestrian bridge was installed in Aberfeldy, Scotland; the first composite reinforced concrete bridge deck built in McKinleyville, West Virginia; and the first all-composites vehicular bridge deck in Russell, Kansas.
Early 2000s
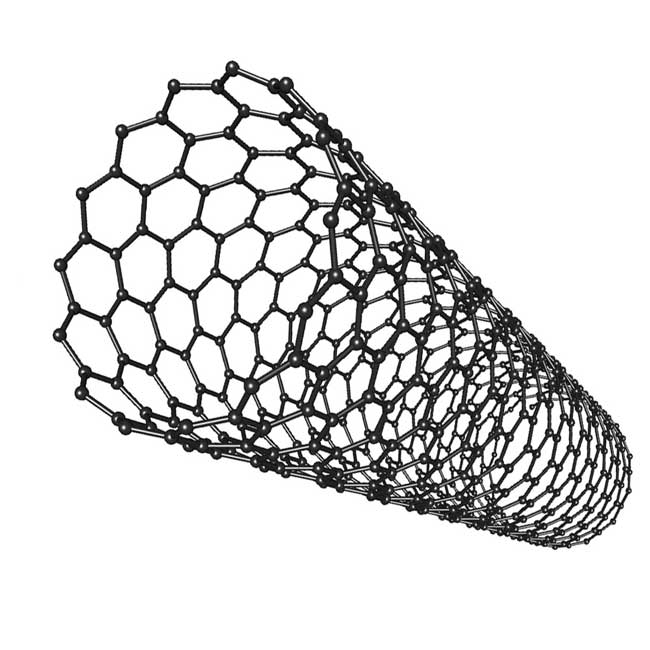
Nanotechnology began to be used in commercial products. Composites play an important role in carbon nanotubes to improve the mechanical, thermal and electrical properties of the bulk product.
2010s
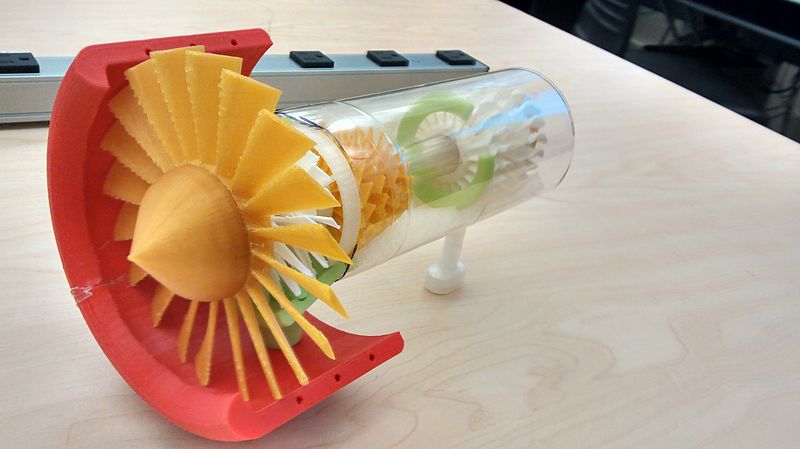
Composite companies are jumping on the 3-D printing train by printing items with reinforced fibers. Fiberglass is most frequently used to reinforce plastics in 3-D printing process across every market sector, including automotive, aerospace, tooling, medicine and infrastructure.
2014
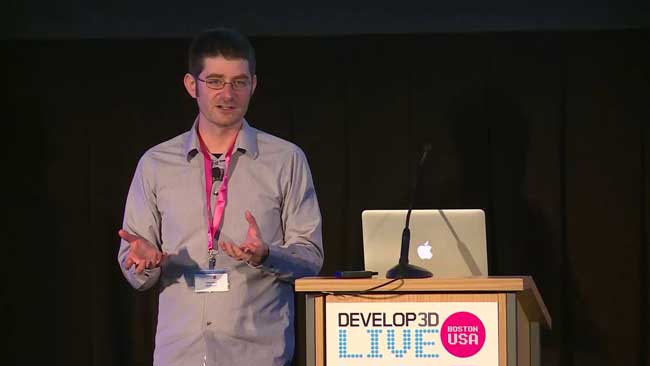
MarkForged announced the world’s first carbon fiber 3-D printer.
2015
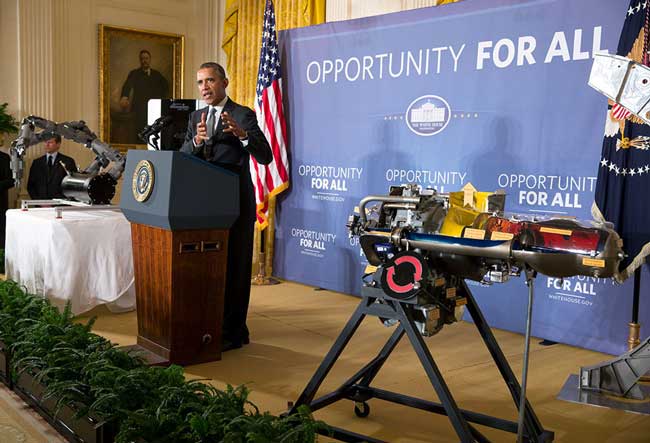
The U.S. Department of Energy announced the Institute for Advanced Composites Manufacturing Innovation (IACMI), a $259 million public-private partnership. The Institute will focus on making advanced composites less expensive and less energy-intensive to manufacture, while also making composites easier to recycle.