Composites vs. Other Materials
Traditional materials like wood, steel and concrete have held a stronghold in the infrastructure market for centuries. However, composites has many significant advantages when it comes to infrastructure applications like bridges, utility structures, pipes and tanks.
Composites offer light weight, corrosion resistance and design flexibility. In retrofit and rehabilitation situations, composites extend the service life of the bridge, are faster to install and require minimal disruption to the structure. Over the past 20 years, these properties have convinced engineers across North America to build more than 500 bridges with composites.
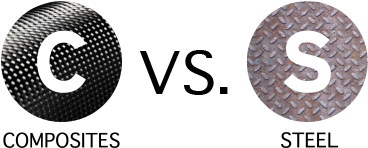
In addition to corrosion resistance, Composites have a number of other advantages over steel, including:
- Light Weight: A cubic foot of cast steel weighs approximately 490 pounds. Depending on the material formulation, composites can be up to 70 percent lighter.
- High Strength and Durability: They can be custom-tailored to add strength in critical areas, such as spots that may bend or wear out. With steel, if greater strength is needed in any area then more metal must be added, which in turn increases weight.
- Low Maintenance: Engineers can use composites to reduce maintenance costs due to their resistance to deicing salts and other corrosive agents.
- Large Part Geometry: A single piece made of composites can replace an entire assembly of metal parts, streamlining the production process and reducing lifetime maintenance.
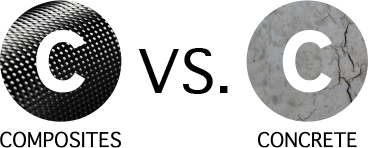
In addition to steel, many of today’s bridges feature a great deal of concrete. For decades, concrete has been the premier material used to construct bridge decks. However, as the industry has shown, there are numerous benefits to using composites instead of concrete, such as:
- Efficient Installation: Bridge deck panels constructed with composites are easier, faster and less expensive to install than concrete panels. Poured concrete takes 28 days to cure and precast concrete panels require the use of heavier duty equipment. Precast concrete panels require the use of heavier duty equipment. And because a single tractor-trailer can handle a larger number of panels, transportation costs are reduced.
- Less Maintenance: Non-slip, high-traffic polymer aggregate overlay has a life cycle of 15+ years without repair. Extreme damage can be patched, while concrete requires more frequent repairs. Additionally, concrete's broom finish wear surface requires regular upkeep. FRP’s polymer concrete’s quartz aggregate gives its wear surface the same friction and feel as a conventional broom finish.
- Increased Lifespan: Concrete might last anywhere from 15-50 years. Salt and coastal environments dictate more costly concrete products. Chemicals also shorten the life of a concrete product. Composites last more than 75 years, is resistant to water, salt, chemicals, hot and cold temperature extremes and variables found in coastal environments.
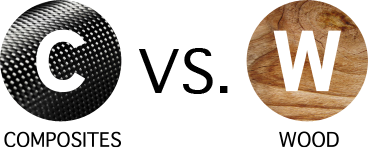
In many of today’s utility structures, wood is often the go-to material. Wood is actually a natural composite – a combination of cellulose fiber and lignin. Some composite applications, including fishing poles and golf club shafts, copy the natural design of woods such as bamboo. But manmade composites have clear-cut advantages over wood, such as:
- Durability: Wood eventually rots, but composites are durable. Think about the marine industry: wooden boats require considerable care to last an owner’s lifetime, while many composite boats remain afloat for 50-plus years with routine maintenance.
- Dimensional Stability: Composites retain their shape and size when they are hot or cool, wet or dry. Wood, on the other hand, swells and shrinks as the humidity changes.
- Light Weight and Easy Installation: Because they are lightweight, composites are an ideal replacement for wood in applications such as utility poles: they cost less to transport and are simpler to install in remote locations than their wooden counterparts.
- Termite Resistance: Termites, carpenter ants, beetles and other pests eat away at wood, causing extensive damage. Composites are pest-free, making them ideal for everything from window frames to retaining walls.