Composites vs. Other Materials in Industrial Applications
Unless protective measures are taken, buried steel tanks, piping, and other metal components of fuel storage systems corrode and eventually leak products into the environment. Corrosion can attack the metal either over the entire surface of the metal (uniform corrosion) or in a small, localized area, creating a hole. Localized corrosion can perforate an unprotected tank in about 15 years and is the most common form of corrosion.
To prevent this from happening, many manufacturers now make pipes and tanks with noncorrodible material such as fiberglass. FRP composites do not rust or corrode. There are various resin systems available to the fabricator which provide long-term resistance to almost every chemical and temperature environment. Properly designed composites parts have long service life and minimum maintenance as compared to most competitive materials.
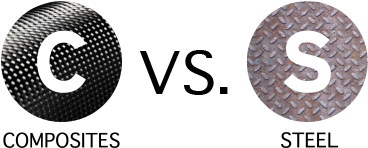
- Corrosion resistance : Perhaps the most highly valued property of composites in industrial applications is their ability to stand up to severe weather and wide temperature ranges. While steel rusts easily and is often coated with zinc, composites are naturally anti-corrosive.
- Inherent durability : There are case histories of fiberglass ductwork being in service in chemical manufacturing plants for over twenty-five years – operating in harsh chemical environments twenty-four hours a day, seven days a week.
- Lightweight : Composites can deliver more strength per unit of weight than most metals. In the case of steel this comparison is drastic since a cubic foot of cast steel weights approximately 490 pounds. Composites can be up to 70 percent lighter than steel.
- High strength : Composites can be designed to provide a vast range of mechanical properties including tensile, flexural, impact and compressive strengths. FRP composites are not isotropic, but anisotropic which allows the designer/fabricator to design a laminate with oriented reinforcement to provide strengths in specific areas or direction as the final application requires.
- Part Consolidation: A single composite part can replace a number of steel parts, reducing cost, assembly time and maintenance.
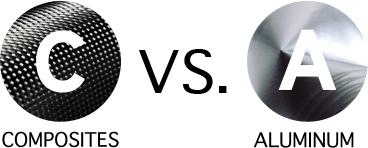
- Corrosion resistance : As outlined above, this is the primary advantage composites offer for industrial applications. Aluminum simply cannot match the naturally corrosion resistant quality of composites.
- Lightweight: While Aluminum is the lightweight option among metals, composites are consistently lighter than aluminum, without giving up any of their high strength property.
- High strength: Composites can be designed to provide a vast range of mechanical properties including tensile, flexural, impact and compressive strengths. FRP composites are not isotropic, but anisotropic which allows the designer/fabricator to design a laminate with oriented reinforcement to provide strengths in specific areas or direction as the final application requires.
- Design flexibility : Unlike aluminum, composites can be molded into virtually any shape.
- Part consolidation : One composite part can cover multiple aluminum parts, creating cost reductions on the up front assembly time and back end maintenance.