There are two major groups of resins that make up what we call polymer materials—thermosets and thermoplastics. Thermoset resins are used to make most composites. Unlike thermoplastics, they are converted from a liquid to a solid through a process called polymerization, or cross-linking. When used to produce finished goods, thermosetting resins are “cured” by the use of a catalyst, heat or a combination of the two. Once cured, solid thermoset resins cannot be converted back to their original liquid form. Thermosets cross link during the curing process to form an irreversible bond.
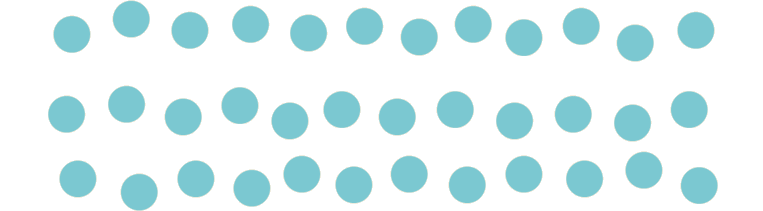
The thermoset resins used in composites include:
Polyester
Highly Versatile – 75% of All Resins Used
- Balance of properties
- Faster cure / better handling
Unsaturated polyester resins (UPR) are the workhorse of the composites industry and represent approximately 75% of the total resins used. A range of raw materials and processing techniques are available to achieve the desired properties in the formulated or processed polyester resin. Polyesters are versatile because of their capacity to be modified or tailored during the building of the polymer chains. They have been found to have almost unlimited usefulness in all segments of the composites industry. The principle advantage of these resins is a balance of properties (including mechanical, chemical, and electrical) dimensional stability, cost and ease of handling or processing. Polyester producers have proved willing and capable of supplying resins with the necessary properties to meet the requirements of specific end user applications.
Epoxy
Strong properties, more complex processing
- Low shrinkage
- Corrosion & temperature resistance
- Superior mechanical, electrical properties
- Excellent substrate adhesion
Epoxy resins have a well-established record in a wide range of composites parts, structures and concrete repair. The structure of the resin can be engineered to yield a number of different products with varying levels of performance. A major benefit of epoxy resins over unsaturated polyester resins is their lower shrinkage. Epoxy resins can also be formulated with different materials or blended with other epoxy resins to achieve specific performance features. Epoxies are used primarily for fabricating high performance composites with superior mechanical properties, resistance to corrosive liquids and environments, superior electrical properties, good performance at elevated temperatures, good adhesion to a substrate, or a combination of these benefits. Epoxy resins do not however, have particularly good UV resistance.
Vinyl Ester
Combination of polyester and epoxy properties
- Mechanical strength, corrosion resistance
- Better handling / faster cure
- Easier processing / handling / fabrication than epoxy
Vinyl esters were developed to combine the advantages of epoxy resins with the better handling/faster cure, which are typical for unsaturated polyester resins. These resins are produced by reacting epoxy resin with acrylic or methacrylic acid. This provides an unsaturated site, much like that produced in polyester resins when maleic anhydride is used. The resulting material is dissolved in styrene to yield a liquid that is similar to polyester resin. Vinyl esters are also cured with the conventional organic peroxides used with polyester resins. Vinyl esters offer mechanical toughness and excellent corrosion resistance. These enhanced properties are obtained without complex processing, handling or special shop fabricating practices that are typical with epoxy resins.
Phenolic
High temperature, insulation properties
- Creep resistance
- Thermal insulation
- Corrosion resistance
- Sound dampening
- Excellent fire/smoke resistance
Phenolics are a class of resins commonly based on phenol (carbolic acid). Phenolics are thermosetting resins that cure through a condensation reaction producing water that should be removed during processing. Pigmented applications are limited to red, brown or black. Phenolic composites have many desirable performance qualities including high temperature resistance, creep resistance, excellent thermal insulation and sound damping properties, corrosion resistance and excellent fire/smoke/smoke toxicity properties. Phenolics are applied as adhesives or matrix binders in engineered woods (plywood), brake linings, clutch plates, circuit boards, to name a few.
Polyurethane
Tough, flexible, good adhesion
- Abrasion resistance
- Impact resistance
- Chemical resistant
- Good substrate adhesion
- Rapid curing
Polyurethane is a family of polymers with widely ranging properties and uses, all based on the exothermic reaction of an organic polyisocyanates with a polyols (an alcohol containing more than one hydroxyl group). A few basic constituents of different molecular weights and functionalities are used to produce the whole spectrum of polyurethane materials. Polyurethanes appear in an amazing variety of forms. These materials are all around us, playing important roles in more facets of our daily life than perhaps any other single polymer. They are used as a coating, elastomer, foam, or adhesive. When used as a coating in exterior or interior finishes, polyurethanes are tough, flexible, chemical resistant, and fast curing. Polyurethanes as an elastomer have superior toughness and abrasion in such applications as solid tires, wheels, bumper components or insulation.