What are Composites
The definition of a “composite” is two or more materials with markedly different physical or chemical properties – categorized as “matrix” or “reinforcement” – combined in a way to act in concert, yet remain separate and distinct at some level because they don’t fully merge or dissolve into one another.
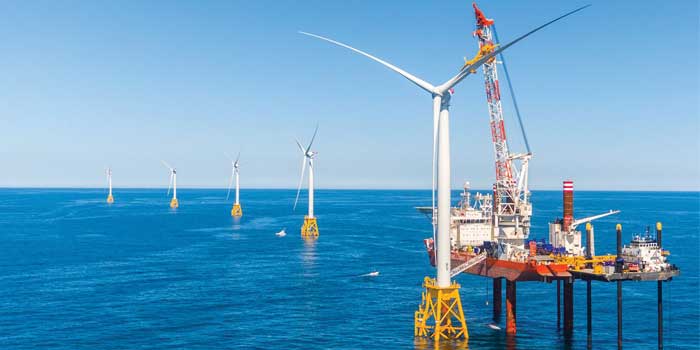
While other materials are technically composites, this term has come to refer to a combination of resin and fiber reinforcement, sometimes called “fiber-reinforced polymers” or FRP composites. This combination can produce some of the strongest and most versatile materials for their weight that technology has ever developed.
Moreover, the resin, fiber and additives that comprise composites can be adjusted to produce final parts and products with a wide range of physical properties, lending composites to a myriad of applications.
While the resin used in composites is sometimes referred to as “plastic,” it is not to be confused with most plastics we see today, which are actually pure plastic, like toys and soda bottles.
Why Composites?
Composites provide unique benefits over traditional materials such as steel, aluminum, wood or concrete. This is owed to both the unique nature of the material, and our ability to adjust their components to change the characteristics of the final product. As a result, composites provide many advantageous physical properties and great design flexibility. For more about the benefits of composites explore their application in various industries:
The benefits of composites include:
- Lightweight
- High strength
- Corrosion resistant
- High strength-to-weight ratio
- Directional strength - tailor mechanical properties
- High impact strength
- High electric strength (insulator)
- Radar transparent
- Non-magnetic
- Low maintenance
- Rapid installation
- Long-term durability
- Parts consolidation
- Dimensional stability
- Small to large part geometry – styling/design – sculptural form
- Customized surface finish
Composites in the Making
Composites have the ability to open up a world of new possibilities for manufacturers, designers and engineers. As many companies have learned, working with composites allows you to tailor the properties of fibers, resins and additives to get the exact material properties and performance characteristics you need. As composite materials have become more sophisticated, so too have the manufacturing processes used to make products with composites. Once novel methods like pultrusion, resin transfer molding and large-scale filament winding have now become mainstream in the composites industry.
Materials
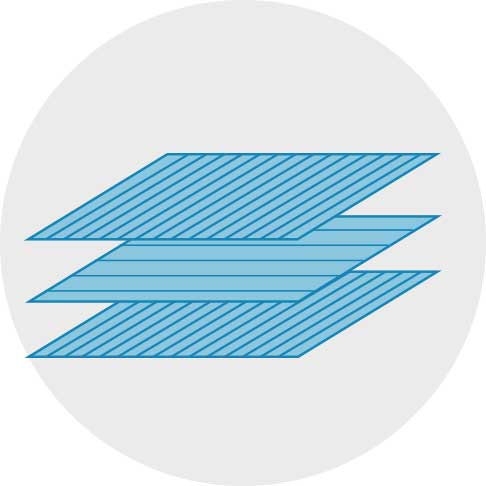
Fiber
Fiber reinforcement such as glass, carbon, aramid or other reinforcing material such that there is a sufficient aspect ration (length to thickness) to provide a discernable reinforcing function in one or more directions.
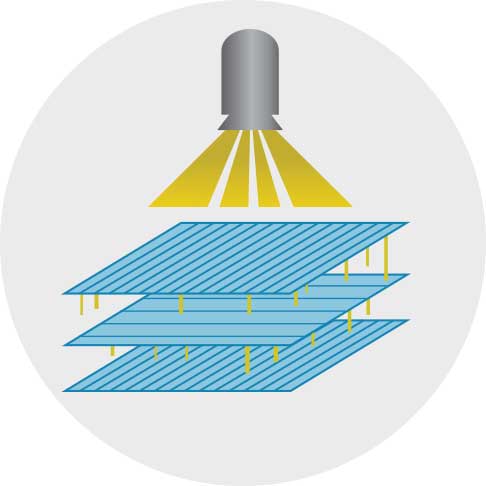
Resin
Polymer matrix resin, either thermoplastic or thermoset, such as polyester, isopolyester, vinyl ester, epoxy, phenolic.
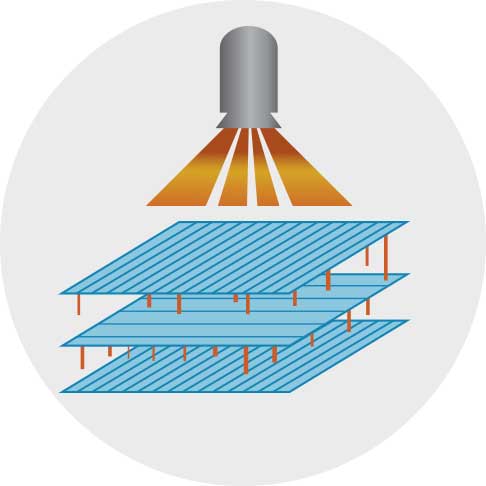
Additive
Fillers, additives, core materials are added to composites to control the molding process or enhance the physical properties of the final product (color, strength, durability, fire resistance, and many more characteristics).
Processes
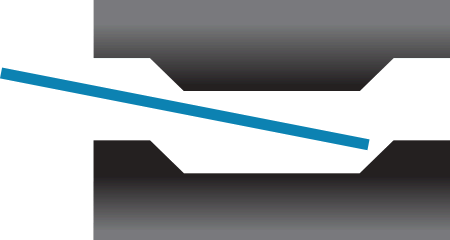
Molding processes shape composite materials into a vast range of products and parts. A key additive is a catalyst that initiates the chemical reaction that causes the resin to “cross-link” and become solid (cure).
The more flexible resin, or matrix, provides shape, protects the fibers and transfers the load between the fibers. The fibers, in turn, provide strength and stiffness to reinforce the matrix and help it resist cracks and fractures.
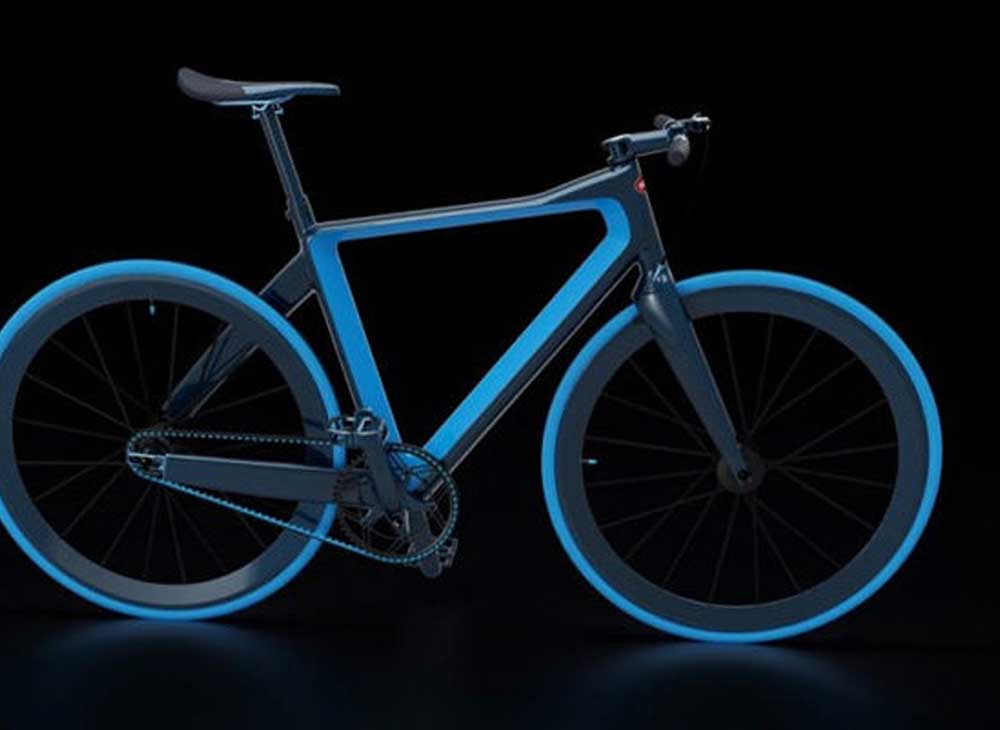
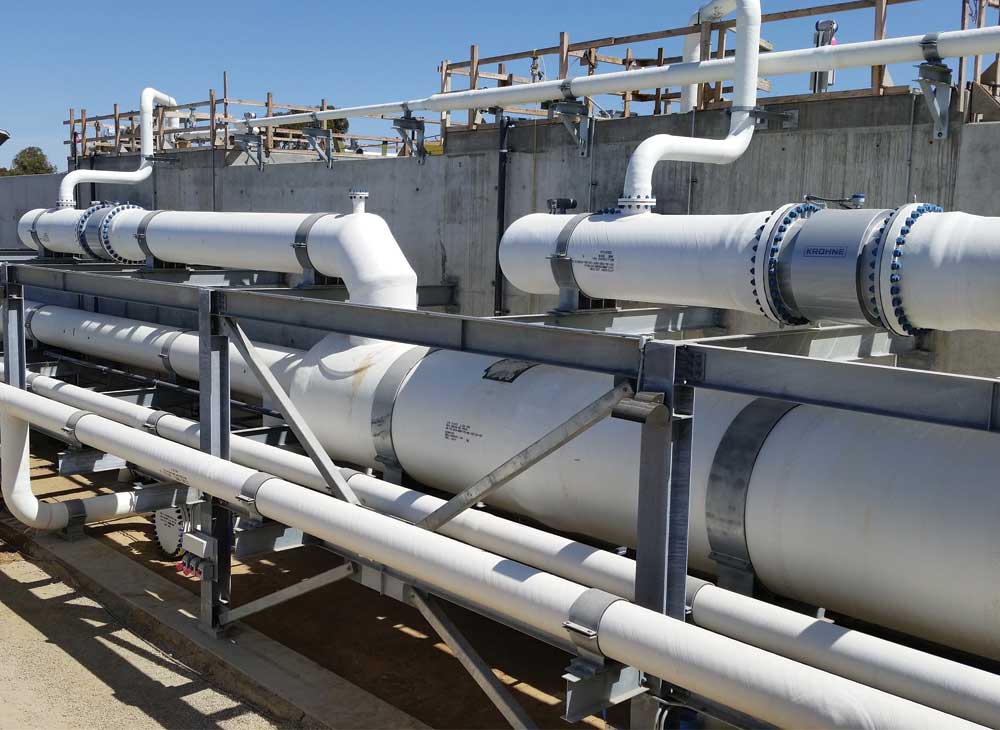