Debunking Myths about Composites in Transportation Markets
Composites offer significant advantages to the diverse transportation markets. From automobiles and aircraft to buses and rail applications, the benefits of lightweight and durable composites are providing fuel savings and design and manufacturing efficiencies across the transportation spectrum. According to ACMA’s 2017 State of the Industry report, aerospace and automotive are two of the most promising areas of growth for composites, primarily due to the global economy’s shift toward lightweighting to meet emission reduction goals and increase fuel efficiency.
However, in comparison to other industries that have embraced composite technology, the approval process for new materials in aerospace takes a significant amount of time and opportunity cost is high. Industry forecasts predict annual growth rates of 6 to 9 percent for automotive composites over the next several years. However, there remains plenty of misinformation about composites that could impeded greater adoption in transportation, including:
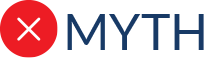
Composites can’t help OEMs cut costs
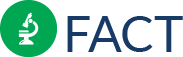
With the current trend towards niche marketing and frequent design "freshening" production runs of closure panels are typically shorter. Thus, it is advantageous to minimize both the number and cost of the tooling as it will be amortized over fewer units. Tooling for composite parts can be as much as 80% less than comparable metal parts. Steel parts often require a series of stamping dies to produce a desired shape in addition to multiple components that must be subsequently assembled. In most cases, one or two molds and presses take the place of entire multi-station stamping lines. All of these factors lead to lower costs, tighter tolerances and less assembly required.
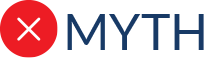
Composites make manufacturing too complex
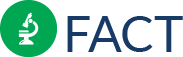
Finished assemblies with fewer parts cut manufacturing costs and often accelerate design completion and model introduction. A single composite molding can take the place of up to 15-20 individual steel components and fasteners. With fewer components to procure, inventory and assemble the net result is tighter tolerances, better fit & finish and reduced labor cost.
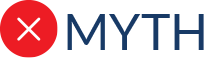
Composites can’t handle impact
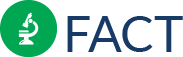
Composites' dent and ding resistance is far superior to that of steel, aluminum and thermoplastic panels. Their Coefficient of Linear Thermal Expansion (CLTE) is very similar to steel which allows them to maintain excellent fit and finish over a wide range of temperatures. They do not embrittle when exposed to cold temperatures nor will they melt in the presence of extreme heat.
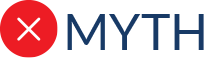
Composites are difficult to repair
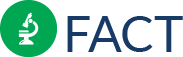
Damage to composite components is not always visible to the naked eye, but the concept of repair of composite structures is not always difficult. With composites, a smaller damaged area can be isolated, cutout and repaired, unlike metal bodies where bent steel or aluminum often requires full section repairs.
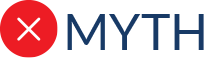
Composites can’t be recycled
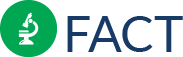
All over the world, various businesses, associations and coalitions are working to make composite recycling a viable solution. Roughly 10 percent of the CFRP used in BMW i series vehicles is recycled material. Additionally, Boeing has been working with various stakeholders to recycle CFRP parts from its 787 program.